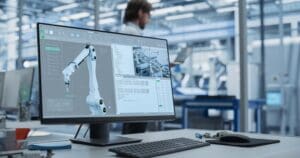
There’s a quiet shift happening across UK manufacturing floors, and it’s not all about robots or AI algorithms pulling headlines. While the tech press stays busy covering quantum experiments and sci-fi-esque automation, the real action is unfolding in more grounded, practical spaces.
It’s not dramatic. It’s not loud. But it’s changing the way things get made—and who gets to make them.
UK manufacturers, long caught between the pressures of offshore competition and post-Brexit supply chain headaches, are finding new footing by rethinking how they produce goods in the first place. The playbook isn’t about outpacing global giants. It’s about tightening up operations, working smarter with what’s already here, and building systems that can move quickly without falling apart under pressure. It’s manufacturing with its boots on the ground—and its eyes fixed on resilience.
No More Waiting Games
One of the clearest signs of progress is how much faster design turns into a product. Prototyping timelines that once dragged for months now wrap up in weeks. The magic isn’t in flashy front-end innovation—it’s buried in the back end. UK firms are tapping into better tooling partnerships, smarter CAD workflows, and modern fabrication techniques that let them move quicker without bleeding quality.
Processes like injection moulding are playing a bigger role here. Instead of shipping designs out to Asia and praying they come back on time, more British firms are keeping it local. Moulds can be cut, tested, and put into production with fewer middlemen, less margin for error, and far tighter turnaround. The benefits are compounding. Products hit shelves faster, defects are spotted sooner, and entire supply chains become less brittle. It’s not a revolution—it’s a smarter way to survive and scale.
And it’s not just the big players who are winning here. Smaller shops and mid-tier manufacturers—many of them family-owned or regionally based—are quietly using this tech-forward approach to stay competitive without chasing risky expansion. It’s steady, grounded growth, and it’s working.
The Labour Challenge Gets a New Angle
Labour is still a problem—no surprise there. But the solution isn’t to automate everyone out of a job. What’s actually happening is more layered. Yes, some tasks are being handed off to machines. But just as many are being upgraded in place, with staff now learning to operate software-guided systems or work in tandem with cobots. Roles are shifting, not disappearing.
The companies that are doing this well aren’t just throwing equipment at the issue. They’re retraining teams, reshaping shop floor dynamics, and investing in upskilling instead of flat-out replacement. The result? More efficient teams who understand both the equipment and the product. It’s a far cry from the dystopian vision of empty factories full of buzzing arms and conveyor belts.
It’s also helping shift perception. Younger workers—those previously uninterested in “the trades”—are taking another look when they realise the job involves touchscreen control panels, 3D modelling, and real-time performance data. Manufacturing isn’t just welding and assembly anymore. It’s software, logistics, analysis, and decision-making, too. And that makes it a whole lot more interesting to the next generation.
Supply Chain: Tighter, Not Bigger
Post-Brexit, supply chains were left wobbly and exposed. What’s changed is how UK firms are choosing to respond. Instead of overreaching, many are pulling things back in. More regional sourcing, fewer international dependencies, and a willingness to spend a little more upfront in exchange for predictability down the line.
What’s powering this isn’t some nationalistic push for domestic-only sourcing—it’s pragmatism. Suppliers you can drive to are easier to manage than ones halfway across the globe. Especially when timelines matter and a single delay can hold up thousands of units.
The stronger firms are also simplifying SKUs, trimming back options that make production messy or shipping unreliable. It’s less about cutting corners and more about cutting waste—time, money, energy, and complication. There’s a new appreciation for just-enough inventory, smart forecasting, and partners who can flex under pressure.
Output Is the Wrong Metric Now
The number of units moving out the door still matters, of course. But relying on factory output alone as a measure of success is starting to look a bit outdated. What counts more now is how adaptable the operation is. Can the factory pivot? Can it respond to demand shifts without choking? Can it run shorter, more profitable batches without a mountain of waste?
Manufacturers with this kind of agility are the ones being snapped up by investors and eyed by multinationals. It’s not just that they can build things—it’s that they can change what they build without months of retooling. That’s becoming more valuable than brute scale.
Plants that once ran one core product year-round are now managing multiple short runs, tweaking specs on the fly, and using live data to adjust production based on incoming orders rather than historical forecasts. It’s not always tidy. But it works. And when a customer changes a spec on Monday and still wants delivery by Friday, it’s often the difference between keeping a contract and losing one.
The Cost of Innovation Is Dropping
Maybe the most underreported story in UK manufacturing is how accessible it’s become to launch a new product. Small-batch manufacturing no longer requires deep pockets or massive warehouses. With the right digital tools and a few strong production partners, start-ups can move from concept to shelf without betting the farm.
Capital is flowing more easily, too. Regional funds, angel groups, and sector-specific grants are helping bridge the gap for first-time founders and second-stage businesses alike. Investors aren’t just looking for big exits—they’re looking for operational stability, sustainable margins, and teams that understand their cost structure from the start.
What’s working best is a measured approach. No bloated teams. No speculative over-ordering. Just tight forecasting, localised partnerships, and the kind of planning that can actually hold up when the market doesn’t behave. That’s what gives smaller firms a shot—and it’s what’s pulling attention away from the old titans and toward a new tier of operators.
What It Comes Down To
British manufacturing isn’t trying to go viral. It’s not chasing hype. It’s figuring out how to be faster, leaner, and more reliable in a world that doesn’t give much room for error. The tools are better. The strategies are sharper. And the people making it all happen aren’t waiting around for someone else to figure it out.
They’re solving it themselves—one part, one process, one product line at a time. And that, quietly, is what’s keeping the industry moving forward. Not with a bang. But with focus, grit, and a lot more agility than anyone expected.
Read more:
British Factories Are Getting Smarter—But It’s Not Where You Think